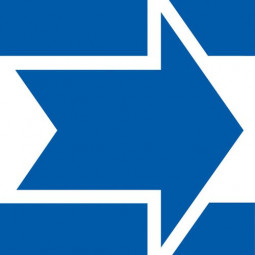
Magnetic Inductive Flow Meter- EPS
The EPS Magnetic Inductive Flow Meter is an advanced instrument designed for the exact measurement of volumetric flow in electrically conductive fluids, such as liquids, slurries, and pastes. Its inline design allows for smooth integration into various industrial processes without disrupting fluid dynamics, as it introduces no pressure drop. Built with versatility in mind, the EPS can be configured with different electrode materials and liners to withstand a wide range of process conditions, including corrosive environments and high temperatures. This makes it an ideal solution for industries such as chemical processing, oil and gas, food and beverage, and pharmaceuticals.
Measuring Process
The EPS Magnetic Inductive Flow Meter depends on the principle of electromagnetic induction to measure flow rates with high accuracy and reliability. The process is broken down into several essential steps:
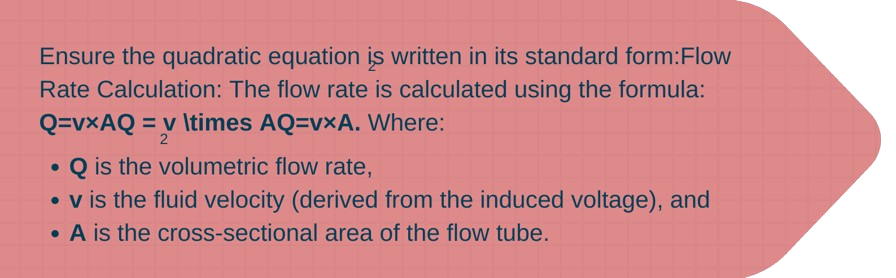
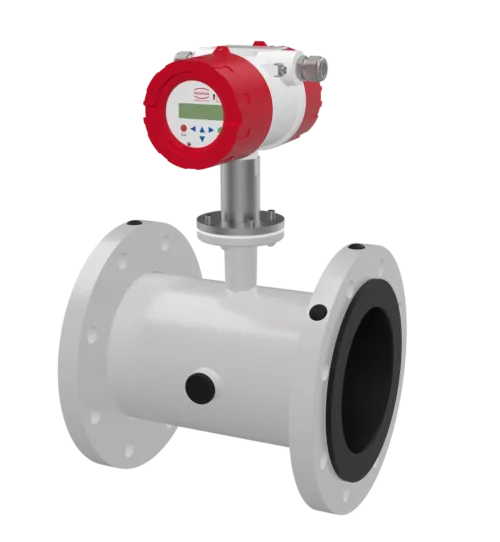
- Magnetic Field Generation: The EPS is equipped with electromagnetic coils that create a stable magnetic field across the flow tube. This magnetic field is perpendicular to the direction of the fluid flow, ensuring that as the fluid moves, it interacts effectively with the field.
- Fluid Flow Interaction: As the conductive fluid flows through the magnetic field, it cuts across the lines of magnetic force. According to Faraday’s Law of Electromagnetic Induction, this movement generates an electric potential (voltage) within the fluid. The amount of voltage generated is directly proportional to the speed of the fluid, meaning the faster the fluid flows, the higher the voltage induced.
- Electrode Detection: Strategically placed electrodes within the flow tube detect this induced voltage. These electrodes are in direct contact with the fluid, ensuring they accurately capture the electrical signal generated by the fluid’s movement through the magnetic field.
- Signal Processing: The detected voltage signal is transmitted to the flow meter’s electronic processing unit. Here, the signal undergoes several stages of filtering and amplification to remove any noise and enhance the accuracy of the measurement. Advanced algorithms then convert the processed signal into a digital flow rate value.
- Output and Display: The calculated flow rate is displayed on the meter’s integrated interface, which can include digital readouts, graphical displays, or external monitors connected to the system. The flow data can also be transmitted to control systems via various communication protocols (such as Modbus, Profibus, or HART) for real-time monitoring and process control.
- Temperature and pressure compensation: In applications where temperature and pressure fluctuations could affect fluid properties, the EPS flow meter may include compensation mechanisms. Integrated sensors monitor these variables, and the system adjusts the flow calculations accordingly to maintain accuracy under varying conditions.
- Data Integration and Control: The EPS flow meter can be seamlessly integrated into larger industrial control systems, allowing operators to monitor flow rates in real-time and make adjustments as needed. This integration is crucial for maintaining optimal process conditions, especially in industries where precise control over fluid flow is essential.
- Maintenance and calibration: The non-invasive nature of the electromagnetic measurement principle means that the EPS flow meter requires minimal maintenance. However, regular calibration checks may be performed to ensure long-term accuracy and to comply with industry standards.
Key Points
- High Precision Measurement: The EPS flow meter offers exceptional accuracy in measuring the volumetric flow of conductive fluids, making it suitable for critical applications where precise flow data is necessary.
- No Pressure Drop: Its inline design ensures there is no pressure loss within the system, preserving fluid characteristics and ensuring efficient process flow.
- Durability: This device is constructed with a variety of electrode materials and liners, allowing it to withstand harsh conditions, including corrosive environments and high-temperature applications. This ensures a longer lifespan and minimal maintenance requirements.
- Low Maintenance: With no moving parts and a robust design, the EPS requires minimal maintenance, reducing downtime and operational costs.
- Versatile Integration: Compatible with various communication protocols, the EPS can be easily integrated into existing control systems, facilitating real-time monitoring and process optimization.
Operational Details
- Electrode Materials: Options include stainless steel, Hastelloy, platinum, and tantalum, catering to different fluid types and process environments.
- Liner Materials: Available liners include PTFE, PFA, and ceramic, allowing the EPS to handle aggressive chemicals and high temperatures.
- Flow Tube Sizes: The EPS is available in various sizes, ranging from DN10 to DN300, to accommodate different flow rates and pipeline diameters.
- Accuracy: The flow meter provides an accuracy of ±0.2% of the measured value, ensuring reliable data for process control.
- Temperature Range: The EPS can operate in temperatures ranging from -20°C to 150°C, depending on the selected liner and electrode materials.
- Pressure Rating: The flow meter is designed to withstand pressures up to 40 bar, making it suitable for high-pressure applications.
- Communication Protocols: Supports Modbus, Profibus, HART, and other industrial communication standards for seamless integration into process control systems.
Details
The EPS Magnetic Inductive Flow Meter is highly versatile and can be applied across a wide range of industries.
- Chemical and Petrochemical Industry: Ideal for measuring the flow of various chemicals, including corrosive acids and bases, within manufacturing processes. Its corrosion-resistant materials ensure longevity in harsh environments.
- Oil and Gas Industry: Used to monitor the flow rates of hydrocarbons, such as crude oil, natural gas liquids (NGLs), and refined products. The EPS helps optimize fuel consumption and manage costs effectively.
- Food and Beverage Industry: Suitable for measuring the flow rates of liquids in beverage production, including water, juices, and other ingredients. It ensures precise control over mixing processes for consistent product quality.
- Pharmaceutical Industry: Essential for measuring and controlling the flow of purified water and other liquids in pharmaceutical manufacturing. The EPS ensures accurate dosing and filling, contributing to product consistency and compliance with regulatory standards.
- Water and Wastewater Treatment: The EPS can be used to monitor the flow of potable water and wastewater, helping to ensure efficient treatment processes and compliance with environmental regulations.
- Diverse Electrode Materials: The EPS offers a wide range of electrode materials, including options for specialized applications, ensuring compatibility with different fluid types and process conditions.
- Customizable Liners: Multiple liner options are available, allowing the EPS to be adapted to specific process requirements, whether dealing with aggressive chemicals or high-temperature applications.
- Inexpensive Grounding Electrode: This device provides an economical alternative to traditional grounding rings by offering a grounding electrode made from special materials, such as tantalum, to reduce costs while maintaining performance.
- High Accuracy: Designed to deliver precise measurements with a high degree of accuracy, the EPS is ideal for critical applications where exact flow data is necessary.
- No Pressure Loss: The flow meter operates without creating any pressure drop in the system, making it suitable for applications where maintaining fluid pressure is essential.
- Wide Range of Process Connections: The EPS offers a large selection of process connections, ensuring compatibility with various piping systems and ease of integration into existing setups.
This comprehensive content outlines the functionality, advantages, and technical aspects of the EPS Magnetic Inductive Flow Meter, making it an excellent choice for industries requiring accurate and reliable flow measurement.
Technical data
Sensor EPS
- Body: Coated steel
- Process connections:
- Steel or stainless steel 1.4301 flanges (EN1092, ASME B16.5 and JIS)
- Food connection DIN11851, TriClamp®
- 2 / 3 / 6 / 10mm inner diameter with process connection G½” (m) or ½” NPT(m)
- others on request
- Lining:
- Hard rubber
- Soft rubber
- PTFE
- EPDM
- Ceramic
- Measuring and grounding electrodes:
- Stainless steel 1.4571
- Hastelloy
- Tantalum
- Platinum
- Grounding ring and other materials on request
- Nominal diameters: DN15 bis DN 1200 (others on request)
- Nominal pressure:
- PN40, ASME Cl150/300 DN15…DN300
- PN16, ASME Cl150 DN50…DN600
- PN10, ASME Cl150 DN200…DN1200
- others on request
- Process temperature:
- -10°C…+70°C EPDM
- 0°C…+95°C Hard rubber (Ebonit)
- -20°C…+150°C PTFE and Ceramic
- Measuring range: 0,5 m/s…10 m/s
- Accuracy: ± 0.3 % of measured value ± 0.01 % * (Q at 10 m/s) (under reference conditions)
- Repeatability: ± 0.15 % of measured value ± 0.005 % * (Q at 10 m/s) (under reference conditions)
- Ingress protection:
- Standard IP67 (EN60529)
- IP68 on request
Transmitter UMF2:
- Installation: integral or remote
- Housing: Aluminum die cast, coated
- Power supply:
- 115/230 VAC 50/60Hz, 10VA
- 24VDC, 10W
- Outputs:
- Analog: 1 x 0/4-20 mA active, galvanically isolated
- Pulse: passive, galvanically isolated, 24V, 60mA
- Status: passive, galvanically isolated, 24V, 60mA
- Ambient temperature: -20 °C to +60 °C
- Ingress protection: IP67 (EN60529), IP68 on request
- Diagnostic Functions: Empty pipe detection, exciter current monitoring
- Communication
- HART® Protocol
Downloads